Types of Welding Gases & What They’re Used For
Last Updated on
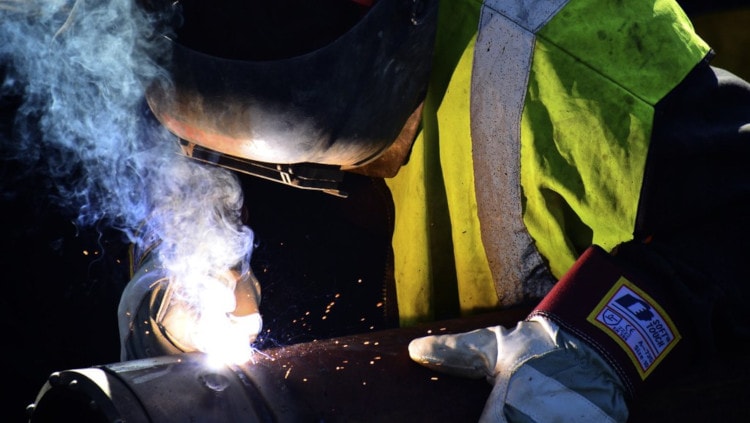
While traditional stick welders knew very little about gases with their welding, the rise of the MIG and TIG welding machines over the last 70 – 80 years has brought in the need for welding gas as a common commodity in most workshops.
Why are there so many different kinds of welding gases, though? And what are they used for?
As we jump into the leading gases and mixtures used in the welding world, it’s fascinating to learn how much we have progressed over the short time since they were first implemented. The progression is enormous, and what’s in store for new gases, or new ways to use these gases, is exciting.
What Is the Purpose of Gas in Welding?
Welding gas is used in a range of different ways. These include shielding the arc from impurities like air, dust, and other gases; keeping welds clean on the underside of the seam opposite the arc (or purging); and heating metal. Blanketing gases are also used to protect metal after the welding process.
Inert and Reactive Gases
Gases come in two categories: inert or reactive. Inert gases do not change or create change when in contact with other substances or temperatures. Reactive gases do the opposite. They react in different circumstances, creating a change of state in the other substances and/or themselves.
Inert gases are useful, as they allow welds to be achieved naturally without unwanted occurrences weakening or distorting the weld. Reactive gases provide a positive change during the process of the weld, which enhances the way the material is fused.
Shielding gas
When air gets into the arc while you’re welding, it causes air bubbles to form within the molten metal, creating a weak and very ugly weld. You cannot MIG or TIG weld without a shielding gas unless the filler material being used is flux-cored or flux coated. This serves the same purpose as a shielding gas, keeping impurities out, but in a different way.
Most shielding gases are inert, which makes them ideal for shielding a welding process as they remain stable under welding’s extreme conditions. They also nurture the weld in different ways, depending on the gas being used, including more penetration, more fluidity when molten, and a smoother surface on the bead.
Purging gas
Purging gases are used to cover the underside of the material you’re welding in the same way a shielding gas does, only it’s done separately from the natural process of the weld.
While you weld the top of a joint, the bottom of the joint is sealed off and has a flow of gas purging it. It’s frequently used with stainless steel items, and it can be the same type of gas or a different gas than what’s used on the top of the joint.
Heating gas
Certain welding, like gas welding and brazing, requires gas to heat the metal or the filler rods to achieve the welding. This replaces the need for an arc.
Specific types of welding require the metal to be preheated before welding, which this gas is used for. The gas is simply a fuel mixed with air or oxygen, which is lit by a flame to warm or melt the metal.
Blanketing gas
Blanketing is a process where tanks and confined spaces are filled with a gas after they’re completed to keep air and other contaminants from damaging or staining the finished product.
Sometimes it’s used to fill the completed projects entirely. Other times, the gas is added to the air-filled tank, creating a mixture to keep the tank pure against other gases or reactions.
What Are the Different Gases Found in a Welder’s Shop?
Argon
Argon is an inert gas, meaning it should not react with other substances. That is what people thought until they found it changes form at high temperature. It’s the third most abundant gas on earth and is brilliant for keeping environments unreactive, for example, in a light bulb to keep the air from consuming the glowing filament.
What is its welding purpose?
Argon is used as a shielding gas to keep air out of a welding arc. It’s used in both the primary welding stage and to purge the backside of the joint. It’s the most commonly used shielding gas and is often found in shielding mixtures for MIG welding operations.
C02
Carbon dioxide is what we exhale when breathing, and it’s also created from organic matter. This makes it a very common gas on earth. Industrial C02 used in workshops and other industrial sites is captured from natural gas and then compressed in a pressure tank.
What is its welding purpose?
C02 is used as a shielding gas. It’s less expensive to buy, but it doesn’t produce the same quality welds as argon does, and it has issues like more spatter during the welding process. This is why it’s more commonly used in mixtures, rather than in its pure form.
Applications using its pure form include flux core welding, some carbon steel MIG welding, and plasma shielding.
Compressed Air
This is the stuff we breathe, but in a compressed form. It’s a mix of 78% nitrogen, 21% oxygen, and 1% other particles. When compressed, a massive volume of air is squashed into a tighter space than it would typically fit into.
It is forced into the tank, creating significant pressure. When it’s released, it comes out with urgency into the application you’re using it for.
What is its welding purpose?
Although air isn’t used in the welding process because it contaminates the weld, it’s used in many other ways in a welding workshop. Many shops use compressed air to clean off dust, swarf, and other dry matter around the workshop. Air nozzles attached to compressors with hoses shoot air out to blow off the dirt.
It’s also combined with fuel to create flames that preheat metal before welding. An even heat transfer or a lower transition from cold to hot is necessary for certain materials while welding, including high carbon steel. This is why preheating is sometimes necessary.
Oxygen
Almost all life is dependent upon this vital gas. It’s odorless, colorless, and tasteless, and many people consider it a more passive and friendly gas than most others. It’s actually one of the most reactive gases in the world. It’s found in most living organisms and combines with every other gas except the inert gases.
What is its welding purpose?
It’s mixed in small quantities of shielding gases to add fluidity to the molten pool and speed to the welding process. It’s used to amplify heat with fuel for gas welding and oxy-cutting metals, and when mixed with acetylene, it creates the only flame hot enough to weld steel.
Gas welding with oxygen also provides a sufficient shield to protect some metals from needing a shielding flux filler wire.
Acetylene
This highly flammable gas is widely used to produce chemicals for other industrial purposes. It’s highly combustible when mixed with air.
What is its welding purpose?
Acetylene is used as fuel for oxy-cutting and oxy-welding. When mixed with oxygen, it’s the most effective gas to form a flame hot enough to cut and weld most metals with ease. It’s more expensive than some other fuel types, but it’s the best type of fuel to use.
Helium
Did you know helium is one of the only substances that doesn’t freeze? Bring its temperature below about 450° F, and it turns into liquid. It’s used in many scientific experiments, and in rockets, decorative and scientific balloons, and hypersonic wind tunnels.
We’ve all had our share of fun using helium with balloons or as a voice modifier, but it’s actually a very precious gas vital to human progression. It’s the second most common gas in the universe, but on Earth, it’s not abundant like other gases and is challenging to produce. Because over six billion cubic feet of it is consumed every year, the supply is gradually diminishing. A few helium-collecting space trips might be necessary soon.
What is its welding purpose?
Helium is used as a shielding gas, in both its pure form and as a mixed solution with other gases in MIG and TIG welding. It provides deeper penetration and brings a higher heat input to welds, but struggles to provide consistent arc starts.
It creates a good mix when used with argon. The argon excels in consistent arc starts, and the helium adds the extra heat needed for specific applications like welding aluminum, and TIG welding in particular.
Nitrogen
As the most abundant gas in our atmosphere, covering close to 80% of the earth’s surface and being a part of every living organism, nitrogen is essential. It’s used to preserve and protect many new products like food, motors, tanks, and anything that could be damaged by too much oxygen or other gases.
What is its welding purpose?
Nitrogen can be used by itself as a shielding gas for laser welding and plasma cutting, and it’s used in some heat treatments. It’s also mixed with other shielding gases for specific applications, but it’s not suitable for carbon steels. When shielding nitrogen-rich metals, it increases the alloy’s mechanical properties and can deepen penetration while stabilizing the arc.
Nitrogen is also used as a blanketing gas once welding is finished inside tanks and enclosed spaces, to preserve the material until it’s used with its intended product.
Hydrogen
As the simplest of all the gases, hydrogen is a fuel that the stars, like our Sun, use to burn. It’s abundant on Earth, easy to produce, and burns without emissions while producing water as its final byproduct.
Aside from being the main element in water, in its raw form, it’s used heavily for commercial purposes. It’s used in food products like peanut butter and oils, and to create essential chemicals such as ammonia.
Photo of Hydrogen
What is its welding purpose?
Surprisingly, hydrogen is used as a shielding gas in mixtures with argon or C02. Some people are frightened by this thought because it’s combustible.
There is a specialized welding process called atomic hydrogen welding, which uses 100% hydrogen in its raw form and produces an arc heat range between 6100° F and 7200° F. This is hotter than an acetylene torch can reach cranking at its hottest. The process is used to weld materials with extremely high melting points, like tungsten. This kind of hydrogen welding is dangerous.
However, due to the percentage of hydrogen used in standard welding procedures, it’s actually very safe. There are risks of weld cracks when hydrogen is used in the shielding gas, but applying protective layers to the weld solves this. Hydrogen is otherwise an excellent shielding gas choice, due to its capacity to produce incredible heat in welds. This increases penetration and makes a much cleaner weld than other gases can produce.
Mixed Gases
There is a vast range of gases to use, all of which excel in specific areas, and are weaker in others. Mixed gases provide a helpful balance to use the strengths of different gases in a harmonized product, offering excellent results.
Some gases are strong in one area and weak in another, so a different gas will be added to compensate for the area lacking. Other gases have numerous properties which, when mixed, result in a gas that uniquely welds a type of material in the desired way. Mixtures include:
Argon and C02
This shielding mix creates a smooth weld with minimal spatter. It ranges from 95% argon/5% C02 to 80% argon/20% C02 mixes. The thinner the section of steel is, the lower a C02 mix is used.
Argon, C02, and Oxygen
Similar to the argon/C02 mix. The welds are clean and the added oxygen, less than 5% of the mix, provides an increase of fluidity in the weld pool and travel speed during the welding process.
Helium and Argon
This helium-rich mix is primarily used for aluminum and other alloys to provide deep penetration and a wide-shaped weld.
Argon, Helium, and C02
A range of different mixes are available, with some dominated by the helium content, and others primarily argon. They’re used with a broad list of various metals, including carbon steel, stainless steel, and aluminum.
Argon and Oxygen
The oxygen content in this mix is small. It’s primarily used for welding light gauge steel and provides assistance with material fusion.
Argon and Hydrogen
This mixture accelerates TIG welding procedures while providing a cleaner weld. The hydrogen deoxidizes the weld from any air that could slip in.
Nitrogen and Hydrogen
A mix blended specifically for shielding austenitic stainless steels. It increases penetration and speeds up the welding process while increasing the stainless steel’s mechanical properties.
Gas Safety
All the gases used in welding have unique dangers according to their characteristics. While most are not flammable, any flammable gas used in a welding shop must be treated with extreme caution, especially acetylene.
Keep flammable gases well away from your welding area unless you’re in the process of using them. When using them, have a class B fire extinguisher nearby. If your extinguisher has no class labeled on it, a class B extinguisher will be filled with either C02 or some sort of dry chemical.
While inert gases pose little threat due to lack of flammability and their not reacting with anything, they can cause asphyxiation if you’re welding in an enclosed space for too long. If you have to weld in a confined environment, make sure to have the right precautions in place. Gas detectors, extractor fans, a welding spotter, and regular breaks are great ways to minimize the danger.
Tanks are designed strong enough to withstand a fair beating and remain intact, but it pays to be cautious hauling your welding tank around. The valve at the top of the tank is a weak point. If it gets smashed off, you can have a severe missile on your hands due to the pressure inside those tanks.
Final Thoughts
Gases are an essential part of every welder’s job. Some welding gases are great in numerous applications, like pure argon for most TIG welding projects, and a mix of argon and C02 for most MIG welding jobs. Knowing the different gases and their purposes will help ensure your welds will be the highest quality possible for their use.
Send us your comments below. It would be great to hear your thoughts.