What’s the Best Gas to Use for MIG Welding?
Last Updated on
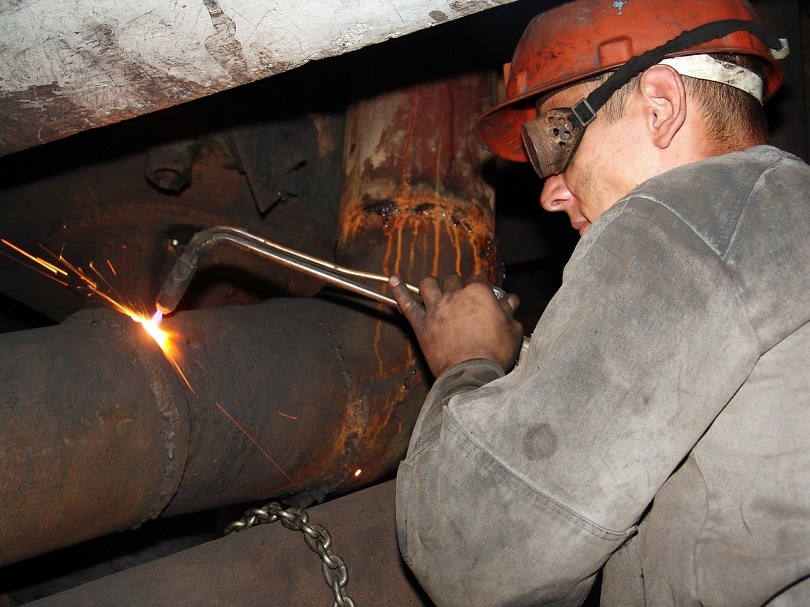
MIG welding utilizes a hand-held gun with a spool-fed cable electrode and a gas nozzle that releases a gas stream to the welding site. This gas stops nitrogen and oxygen contact and other ambient gases with the weld bead. It makes sure that there are strong and consistent results.
Contamination can result in a poor quality weld on your work piece. Therefore, selecting a suitable gas is necessary if you want to achieve the best results. However, what’s the best gas to use in MIG welding?
Regrettably, getting the answer isn’t that simple. Different metals need distinct gas types to get the best results. In numerous instances, a carbon dioxide mix and a 75/25 argon will give you excellent results in many metals. Now, let’s look at some of the choices and discuss how you can select your preferred MIG welding gas for your undertaking. Read on to learn more!
The Best Gas To Use for MIG Welding: What Are the Options?
MIG welding takes place with an arc spawned via a constant solid cable electrode. The electrode is passed via a welding gun and produces a weld pool on the metal surface that connects two parent materials.
The arc is guarded via a shielding gas that’s also passed through the welding gun. The shielding gas also safeguards the weld pool from pollution. Different gases can safeguard the weld pool against environmental pollution. They can be distinguished either as inert or non-inert gases.
Inert Gases (Noble Gases)
Under standard environmental conditions, noble gases are highly resistant to chemical changes. It implies that the shielding weld and arc get the best protection with noble gases.
Helium and argon are the most common noble gases. The two gases are commonly used in TIG and MIG welding.
Most new welders ask, “Can I weld mild steel using argon?”
Yes, you can.
Apart from carbon dioxide, argon is one of the most common shielding gases used in welding. Generally, Argon is used on its own, whether at 100% or combined with one or two other gases to allow deeper penetration into the metal.
You’re assured of a broader but not too deep weld penetration with argon shielding. It’s excellent at maintaining the arc at a stable angle. Helium can form a deeper weld and can produce a hotter burn compared to argon. However, it’s more costly as compared to argon.
Noble gases form much less spatter when welding because they have a higher resistance to chemical reaction than semi-inert or non-inert gases. Helium significantly lessens the weld’s porosity.
However, helium utilizes much more power than argon and needs more care as it may get sultry and lead to overheating and burnouts.
Many welders combine both helium and argon with other inexpensive gases to ensure the costs are down. And because pure argon and helium are only recommended for non-ferrous metals such as copper and aluminum, mixing is also important.
Selecting a Suitable Shielding Gas
Numerous MIG welding applications offer a variety of shielding gas options. You have to assess your welding objectives and applications to select the right one for your particular application.
Welding gases play a crucial role in welding work. They prevent atmospheric gases such as nitrogen, hydrogen, and oxygen from getting to the weld pool. These atmospheric gases can cause issues with the finished weld quality once they get to the weld pool. Therefore, a shielding gas is required.
The question is, which shielding gas are you supposed to use? Argon, carbon dioxide, oxygen, and helium are the four most commonly used shielding gases. Each of them offers unparalleled advantages and disadvantages in every application.
- The price of the gas
- The finished weld characteristics
- Preparation and cleaning after welding
- The parent metal
- Your productivity objectives
The Cost of the Gas
In any manufacturing procedure, the cost is a crucial consideration. Some gases cost more than others. CO2 (carbon dioxide) is the most affordable gas among the four gases used in MIG welding.
You can use it in its pure form and, therefore, you don’t need a secondary gas. It saves you more money.
Characteristics of the Finished Weld
Several parts have to be finished finely. You can clean up others afterward while others don’t need any special finishing requirements. Argon or argon-carbon dioxide mixture is the best option if you want less spatter, better welding action, or flatter bed profiles.
Argon is a noble gas and, therefore, it doesn’t react with molten weld. However, it’s costly. Adding carbon dioxide can reduce costs and still offer agreeable weld quality.
Preparation and Cleaning After Welding
If you’re concerned with preps and cleaning up after welding, an argon and carbon dioxide mixture is the best choice. It offers excellent arc stability, puddle regulation, and lessened spatter as compared to pure carbon dioxide.
The Parent Material
Helium and carbon dioxide offer deep and broad welds and, therefore, are ideal for thick parent materials. Non-ferrous metals such as magnesium, aluminum, and titanium perform best with unadulterated argon.
Helium is an excellent gas with these metals and for stainless steel too. Oxygen does well with mild carbon, stainless steel, and low alloy. However, it leads to corrosion. Therefore, don’t use it with magnesium, copper, aluminum, or any other exotic metals.
Your Productivity Requirements
The mixture of argon and carbon dioxide works well in the spray transfer procedure, which enhances productivity. Another preferred mixture is argon and helium. In this mixture, speed is a factor. It creates a hotter arc that spreads quickly and increases productivity.
Gases Used In MIG Welding
Argon
A mixture of between 75 to 95% argon and 5 to 25% carbon dioxide could be the best choice for firms that stress more on weld quality. It’ll offer a more suitable combination of puddle regulation, arc stability, and lessened spatter than pure carbon dioxide.
With this mixture, you can use a spray transfer procedure that may generate high productivity rates and more visually attractive welds. Argon also creates a narrower penetration profile, that’s helpful for butt and fillet welds.
When welding a non-ferrous metal such as titanium, aluminum, and magnesium, you have to use 100% argon.
- It’s not suitable for steel.
- It’s the best gas for non-ferrous metals.
CO2 (carbon dioxide)
In MIG welding, carbon dioxide is the most common reactive gas. It’s the only gas you can use in its pure form without adding a noble gas. carbon dioxide is also the cheapest among the shielding gases, making it an appealing choice when material costs are the top priority.
Pure carbon dioxide offers deep weld penetration, which is helpful when it comes to welding wide metals. However, it also generates a less steady arc and more spatters than when mixed with other gases. Also, it’s restricted to only the short circuit procedure.
- It penetrates deeper.
- It produces lots of spatter.
- It’s inexpensive.
- You cannot use it with thin metal.
Oxygen
It’s a reactive gas that’s usually used in the ratios of 9% or less to enhance weld pool fluidity, arc stability in mild carbon, penetration, stainless steel, and low alloy. However, it leads to corrosion of the weld metal. Therefore, you shouldn’t use it with magnesium, aluminum, copper, or any other exotic metals.
You cannot use oxygen as a bare gas. However, you can mix it in amounts of 1% to 5% argon and carbon dioxide. It helps improve weld quality.
Oxygen and argon are mostly used for spray transfer on stainless steel to help generate a steady arc. However, the increased fluidity of the weld pool can make out-of-position welding an issue.
- You cannot use it alone as it causes corrosion.
Helium
Similar to pure argon, helium is mostly used with non-ferrous metals and also with stainless steel. Since it generates a broad and deep penetration profile, helium does well with thick metals and is typically used in ratios of between 25 and 75% helium to 75 and 25% argon.
By adjusting these ratios, the travel speed, bead profile, and penetration are changed. Helium generates a “hotter” arc that enables quicker travel speeds and higher productivity rates.
However, it’s the costliest and needs a higher rate of flow as compared to argon. You have to calculate the productivity increase value versus the increased gas cost. When it comes to welding stainless steel, helium is mostly used in a tri-combination of carbon dioxide and argon.
- It’s not commonly used
- It’s the best for non-ferrous metals.
- It’s suitable for thick parent metal.
Advantage of Argon-Carbon Dioxide Mixture And 100% Carbon Dioxide
These two gas mixtures provide users with different benefits and drawbacks. The one you shall use relies on your specific welding purpose.
Argon-Carbon Dioxide Mixture for Shielding
If your shielding gas has a higher percentage of argon mixture, then you’ll have better quality projects.
A 75-25 blend lets you work fast and, therefore, your finished projects will have a much cleaner appearance. The mixture is preferred if you’re working on fragile projects with thinner welds or metals that lie on your structures’ top surfaces.
Several people also increase the ratio of argon and choose the 85%-25% mixture as it offers them a sleeker bead finish.
Nonetheless, there are two issues with a high argon mixture. To begin with, it’s costly. If you’re an expert welder, ensure that your costs don’t exceed the price you ask for your services.
The other issue is that a higher concentration of argon reduces the rate of penetration of the arc. For this reason, welders don’t use unadulterated argon gas for welding. Shielding gases that contain a noble gas, such as argon, aren’t suitable for MIG welding mild steel because they generally lead to an ugly, inconsistent weld seam.
100% Carbon Dioxide for Shielding
If you’re concerned with the cost and don’t want your welds to look their best, you can use carbon dioxide for MIG welding mild steel. It’s significantly inexpensive as compared to an argon mixture and is available at supply retailer stores.
carbon dioxide isn’t a noble gas like argon. However, it provides sufficient chemical protection that’s normally used in MIG welding as a shielding gas. The reaction with the arc generates a “hotter” feeling as compared to the C25 mixture.
It produces a deeper penetration in the connecting metals and creates a strong, larger bead. When used with pure carbon dioxide, the electrical arc isn’t steady. It makes the arc crackle and pops more, forming spatter.
It also forms a mild amount of smoke and fumes when welding. Higher spatter implies that more cleaning is needed after the job is done. You shouldn’t use pure carbon dioxide if you’re welding thinner metal gauges at low Amps. It’s because the arc may blow holes in the frame.
Final Thoughts: How to Choose the Best Gas for MIG Welding
If you’re searching for the best gas to use for MIG welding that has broad application, the 25% carbon dioxide and 75% argon or anything similar to that such as an 80/20 mix, is possibly your best choice.
If you’re on a budget and won’t mind cleaning up a little additional spatter, carbon dioxide is inexpensive at excellent when it comes to experimentation and hobby welding. 100% argon is the way to go for MIG welding aluminum, or generally TIG welding.
With stainless steel, things get more costly when more helium is mixed with argon and carbon dioxide or Oxygen. There, you also have the option of selecting cheaper C2 with a 98/20 mix.
Always take into account the metals you want to weld and ensure that you’re getting the most out of your gas flow. Don’t forget that the key to a dependable bead pattern and avoiding overheating the metal is your preferred gas and your gas’ flow rate.
For gas flow setting and experiment, contact the manufacturer to see what will work best for you and one that will be convenient.
Featured image credit: stafichukanatoly, Pixabay