What’s a Full Penetration Weld? 2024 Guide
Last Updated on
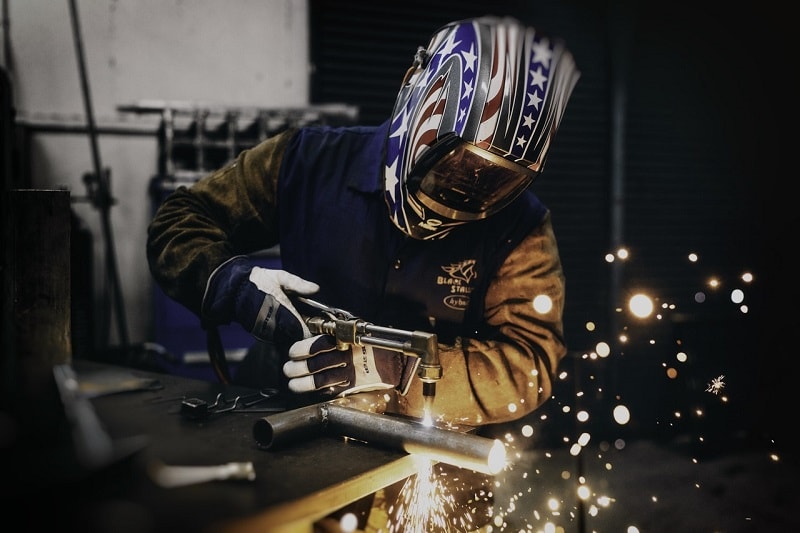
As you know, faults in the welding approach may influence the welded material quality negatively. There are several methods of welding material. In this guide, we’ll tell you more about the full penetration welding approach, also called complete penetration weld.
An Overview of the Process
A complete or full penetration welding approach involves connecting two metal parts, leaving no gaps in between. In this welding type, the filler material infuses the roots of the joint. You can apply this approach to metallic products with high-strain resistance.
In complete penetration weld, metal has a higher strength than in partial penetration. Therefore, metal merchandise with complete penetration is perfect for metal products designed for high strain applications.
If you want to have a thick weld, a full or complete weld penetration is the best bet. You can use different weld passes to bevel and penetrate the weld. Nonetheless, you can attain penetration without a groove bevel in joints with 0.20 inches or greater thickness.
A penetration weld may be a broad weld that has been beveled and penetrated by getting infused with several weld passes. Alternatively, a penetration weld can also be a sheet metal joint that’s 0.020 inches broad that’s perforated. You don’t require a groove bevel.
For deep perforation, you need a high power density. It should be more than one megawatt for every square meter. The outcome is an enhanced welding and stronger metal merchandise.
Metal parts are melted together using a butt weld that blends wholly with the parent metal. The parent metal’s strength is similar across the joints. The complete penetration weld joint can come in distinct forms comprising single and dual-v configurations.
https://www.instagram.com/p/CJZxpoondIG/
If you’ve performed partial perforation welding, the melted metal may have a lower potency resistance factor than the parent metal.
What Variables Influence Weld Perforation?
There are a couple of variables that affect weld penetration. Among them, the crucial ones are:
Voltage
You should know that the lower the voltage, the deeper the penetration. If the voltage is higher, it usually implies that the arc is commonly disseminated. Also, it deposits a broader weld bead.
On that note also, the arc begins reacting unpredictably and loses perforation.
The Velocity of the Wire Feed
The speed at which the anode moves down the weld joint influences the length of time the arc energy must convey into the parent plate at any given point.
As the travel velocity increases time, the arc above the joint shrinks, as well as the perforation.
Polarity
The polarity type influences the perforation level. With the many arc welding procedures, the below types of polarity have the following effects:
- Positive DC Electrode: With the direct current positive polarity, there’s more weld perforation generated. It’s because more arc energy is concentrated into the parent metal.
- Negative DC Anode: With the negative DC polarity, less weld perforation is created as more of the arc energy is concentrated on the anode and not the parent plate.
https://www.instagram.com/p/CELpZuBHnHm/
The Position of the Torch
The welding torch’s position also influences the degree of perforation. However, the influence is somewhat less than the arc travel velocity or the current used in welding. Usually, the backhand welding approach leads to deeper penetration than the forehand welding technique.
Using the backhand welding technique and a 25-degree torch angle, you can attain maximum penetration. Nonetheless, a higher torch angle leads to instability of the arc and, therefore, stops deeper penetration.
The Rate of Deposition
The deposition rate depends on the speed of the wire feed. To attain a specific rate of deposition, you can alter the tip-to-metal distance and the current.
A small distance between the tip and the metal leads to a low wire-feed velocity and high current used in welding. The outcome will be deeper penetration, and the rate of deposition will be minimal. And because less metal will be deposited at a certain current, the penetration will be higher.
A lengthy tip-to-metal distance is appropriate if you want to attain a shallow penetration. It causes a low deposition rate at a certain current. It leads to less penetration.
What are the Advantages of a Complete Penetration Welding?
Full penetration welding offers several benefits as compared to low or incomplete penetration weld. They comprise:
Resistance to Corrosion
If you weld metal using complete penetration, it has higher corrosion resistance. A full penetration weld leads to a melted joint line. On the contrary, the joint line isn’t infused with partial penetration.
https://www.instagram.com/p/BzTR_0qA83A/
The gaps between the joints lead to possible differences that make the metal corrode.
Potent Weld
Like we’ve mentioned above, a complete penetration leads to a much potent weld than partial penetration. In complete penetration, the joint is infused. It leads to an additional volume of the metal leading to higher strain resistance.
On the contrary, with the partial penetration approach, the welds have gaps in the joint line. The gaps focus on the geometric strain.
Full Fusion
A complete penetration weld covers more space. Thicker penetration increases the likelihood of the filler getting to the root. It leads to full penetration. If a partial penetration leads to a narrower penetration profile, there’s a likelihood of incomplete fusion at the root of the metal.
Accomplishing a full fusion at the root of the weld joint is crucial. If the tip-to-metal distance is lengthy, and the anode isn’t aimed at the root well, the lack of fusion can bring about structural problems in the resultant metal product.
So, Is Full Penetration Welding an Effective Technique?
In complete penetration, all of the material between the weld joints is fused. Ensure that you utilize full penetration welds well. This approach is preferred over partial penetration because it produces high-strength metal with higher strain and corrosion resistance.
Also, you should be wary of the drawbacks of deep penetration. They include vulnerability to burnout, weld puddle, and in isolated cases, diluted weld deposits.
We’ve provided you with a guide that’ll help you use suitable welding techniques for any welding project you have.
Check out some of our other top-trending posts:
Featured Image: Pixabay, Unsplash – Free to use (CC0)